Industrial robots and CNC machine tools integrated four major applications
The automotive industry has been the most important fie…
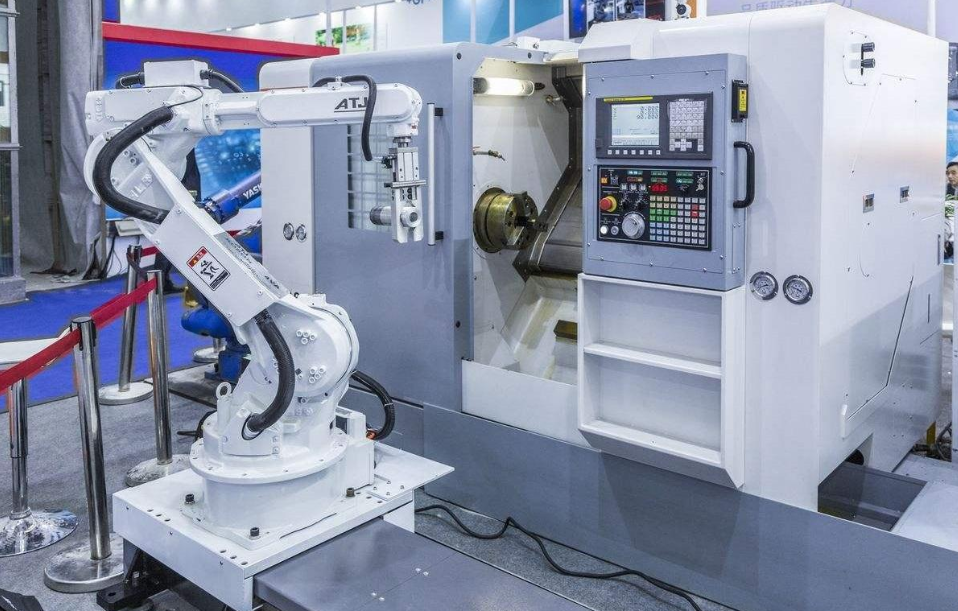
The automotive industry has been the most important field of robot application in the past, with the improvement of automation demand, the application of industrial robots has been greater expansion, in addition to traditional welding applications, robots in the machine tool loading and unloading, material handling palletizing, grinding, spraying, assembly and other fields have also been widely used. Metal forming machine tool is an important part of the machine tool, forming processing is usually associated with high labor intensity, noise pollution, metal dust, etc., sometimes in high temperature and humidity and even pollution in the environment, the work is simple and boring, enterprises are difficult to recruit. The integration of industrial robots and forming machine tools can not only solve the problem of enterprise employment, but also improve processing efficiency and safety, improve processing accuracy, and have a great space for development.
CNC bending machine integrated application
There are two main ways to integrate robot bending. One is the bending machine as the center, the robot is equipped with a vacuum suction cup, magnetic distribution of the loading frame, positioning table, cutting table, turning frame to form a bending unit. The second is the flexible processing line of the plate formed by the robot and the laser equipment or the CNC turntable punch, the industrial robot walking shaft, the plate transmission line, the positioning platform, and the vacuum suction cup gripper. Eston uses its own technology and platform in robot control system and machine tool numerical control system to achieve seamless connection, develop bending software packages, and realize closed-loop control of robot supporting materials during bending. At different bending speeds, the robot can automatically match the complete tracking, and the bending software package can also shorten the bending teaching time from the past 2-3 days to 2-3 hours. It is well used in the processing of switch cabinet, file cabinet, elevator, security door and so on.
Press stamping integrated applications
There are two main ways to integrate robot and press stamping. The first is a single robot stamping and loading: the robot transfers the plate from the unpalletizing table to the positioning table, and then transfers it to the press mold for stamping. After the stamping is finished, the robot takes the material into the stacking table to realize the automatic loading and unloading of the single press robot. The second is the robot stamping connection: the stamping connection is established between multiple presses through multiple robots. According to the forming process requirements of the workpiece, it is necessary to cooperate with several presses for processing. The whole production line is composed of the unstacking robot, the feeding robot, the transfer and handling robot between the press and the tail line robot. Compared with the robot with linear coordinates, the industrial robot is more flexible, has no equal requirements for the mold, and is easy to integrate. Eston uses the autonomous press control system and the robot control system to seamlessly connect, so that the robot's action and the press to achieve the best coordination, the use of fieldbus, to maximize the efficiency of the entire production line, higher safety
Integrated application of hot die forging
A hot die forging line usually consists of two die forging presses, one for stamping and the other for trimming. The hot die forging robot integrated application is usually configured with two robots, one is responsible for transferring the high temperature material after the intermediate frequency furnace treatment to the stamping die forging press, and the other is responsible for transferring the material from the stamping die forging press to the other die forging press for cutting. In order to prevent the high-temperature stamping workpiece from sticking to the mold, it is necessary to lubricate the mold with graphite after each stamping, and the lubrication can be done by a robot or can be achieved by a specialized mechanism. Because the forging is high temperature and humidity and the harsh environment brought by graphite lubrication, special attention should be paid to the protection work of the robot and the ability of the robot itself to resist thermal radiation, the 4-5-6 axis motor of the robot of Eston Company has the structural characteristics of self-away from thermal radiation at the connection of the robot arm and the forearm. The electronic CAM control system is installed in the die forging press to coordinate the operation of the die forging press with the operation of the robot, improve the processing efficiency and improve the safety of the system.
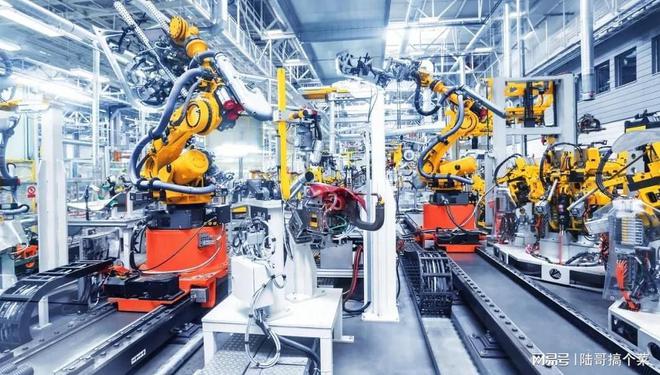
Welding application
Welding is the process after the sheet metal processing of the forming machine tool. There are two types of robot welding: resistance welding and arc welding. The application of welding robot accounts for more than 40% of the entire robot application. The application of arc welding is based on the robot as the core, and the welding workstation is composed of welding machine, wire feeder, welding gun and fixture. Eston offers dedicated arc welding robot workstations of 6kg with arm lengths of 1400, 1600 and 2000mm. The resistance welding application is based on the robot as the core, and the spot welding workstation is composed of spot welding gun, welding controller, moisture unit, pipeline package, fixture, etc. Eston can provide 220kg, arm length 2600mm dedicated resistance welding robot workstation. In addition, Eston Automation develops specialized welding software packages for welding applications, integrating a library of welding expert process parameters into robotic systems for all types of needs.
Robots are a typical representative of advanced manufacturing technology and automation equipment, and intelligent industrial equipment has become the basis for the upgrading and transformation of global manufacturing. The integrated application of industrial robots and CNC machine tools makes intelligent manufacturing and digital workshops and intelligent factories move from concept to reality.