Food and Beverage Industry: Why Bearing Materials Matter
The Food and Beverage Industry is large, diverse, and full of specialized machinery.
It’s one of the oldest industries on the planet, but still full of innovation. From new products to higher-volume, lower-cost production techniques, this industry is always looking for new ways to produce the food consumers want at the best possible price. And vital equipment is there every step of the way. From simple ovens and conveyor belts to complex bottling and packaging machines, the food and beverage industry depends on equipment for industrial-scale food production.
In this article, we provide a brief overview of this essential industry and look at the unique challenges its equipment presents for components like bearings. Finally, we take a look at how TriStar has used our materials expertise to solve engineering pain points for Food and Beverage companies. Advanced polymers and composites are a powerful solution for clean, greaseless operation in food processing and packaging facilities.
Food and Beverage Industry Overview
The Food and Beverage Industry includes all the companies involved in transforming raw agricultural goods into consumer food products.
The overall industry supply chain includes food processing, packaging, and distribution. It does not cover raw food production, which falls into the closely related agriculture industry.
This industry includes fresh food, packaged food, and beverages (both alcoholic and non-alcoholic). From food sold at the grocery store to cooked meals served at restaurants, institutions, and events, this industry serves a huge variety of retail outlets.
Examples of Food and Beverage Processing
- Turning fresh milk into anything from dehydrated power to a fine cheese.
- Processing whole plants like carrots into diced or cut packaged goods.
- Transforming grain into flour and then a variety of baked goods.
- Butchering pig, cows, chickens, etc. (A single plant, for example, can process 1000’s of cattle in a single day).
- Adding chemical components like preservatives to enhance shelf life and reduce spoilage. Nutrient fortification is another prominent example.
- Using proteins to manufacture the new wave of synthetic meats: a great example of how this industry creates not only new products but whole new product categories.
All of these processes come with urgent packaging and distribution timelines, often with an imperative to complete the process, with processed food out the door, in under 48 hours from receiving raw food from the farm.
Food and Beverage Industry Pain Points
While different food categories require very different production processes, some challenges are broadly shared in the industry.
The food and beverage industry is tasked with solving some unique business challenges:
- A time-sensitive supply chain where the product can go bad fast. This reality means food companies are always on a schedule, need to plan for specialized storage and transportation, and have to practice careful inventory control.
- A manufacturing production environment with unique demands for hygiene and safe food handling. This imperative includes everything from exhaustive equipment cleaning requirements to tight controls and potential allergens.
- A highly regulated industry that needs to carefully ensure production practices are up to code.
- A tendency toward price-sensitive products where every margin matters.
Pain Points and Solutions for Food and Beverage Industry Equipment
For packing and processing equipment alike, better equipment performance has real business value for food and beverage companies. First, downtime can be extremely costly in this time-sensitive industry: reliability is essential. Second, efficiency matters for this competitive, margin-sensitive industry. Faster, higher-volume machines are important for a wide variety of food processors. Third, a failure to stay compliant with regulations can result in lost production, fines, or even legal liability.
When looking for increased performance for its equipment, this industry has to pay attention to some unique environmental concerns. These concerns are especially important for key mechanical components like bearings.
- Food processing can include a wide variety of temperature conditions, ranging from a flash-freezer to an industrial-scale fryer or oven. Materials need to be carefully selected for performance characteristics at these temperature extremes.
- The heightened cleaning requirements for food processing and packaging equipment mean extremely powerful cleaning agents must be used. These cleaning chemicals are so caustic that they can damage many materials. Materials need to be carefully selected to reflect cleaning agents that will be used. UV treatments are another potentially damaging cleaning process. Selecting the right materials is important for avoiding contamination from grease, ensuring amenability to caustic cleaning chemicals, and avoiding overly porous materials where microbes can hide.
- Dry food products like grains, beans, and sugar are abrasive to hardware and bearing materials. Particulate matter can also be generated in food production of many types. This “food dust” can easily get into the inner working of exposed machines, causing damage and reducing reliability. Sticky grease for traditional metal bearings can exacerbate this problem, functioning almost like flypaper for contaminants.
- Equipment needs to be approved by all relevant regulators. We list some of the most important below.
Important Regulations for Food and Beverage Industry Equipment
- Food and Drug Administration (FDA): regulates the composition, additives, and properties of materials for food contact
- US Department of Agriculture (USDA): regulates food safety and inspection for manufacturing, packaging, and handling practices, including meat, poultry, fruits and vegetables
- National Sanitation Foundation (NSF): an independent agency devoted to achieving solutions relative to public health and the environment
- 3-A Sanitary Standards: an independent agency dedicated to advancing hygienic equipment design for the food, beverage, and pharmaceutical industries
Bearings for the Food and Beverage Industry
Bearings (along with related components like bushings and wear pads) are essential components within food industry equipment. They’re a great example of a crucial component that needs to carefully address each of the pain points listed above while helping equipment operate as effectively as possible.
Traditional metal bearings need to be regularly lubricated with grease. This lubricant presents both a regular maintenance demand, a magnet for particulate matter, and a chronic risk for contamination. Meanwhile, the wrong plastics can deteriorate quickly in the face of caustic cleaning agents.
TriStar has had extensive success using our advanced materials to address all of these issues. Our self-lubricating design puts an end to messy grease. And, we offer a wide variety of materials that are capable at a range of operating temperatures.
Advantages of TriStar Polymers and Composites for Food and Beverage Industry Equipment
- Self-lubricating design eliminates the need for expensive food-grade grease on equipment components. No grease means a more sanitary food production environment, and no spending on lubricant.
- Self-lubricating bearings also mean less maintenance and fewer stoppages for cleaning and re-lubrication.
- Vibration and impact resistance help handle heavy loads and keep conveyors rolling at optimum speeds. Transferring less vibration throughout the machine can be beneficial for the service life of other components as well.
- Superior strength and wear resistance for extended use in a demanding, 24/7 processing and packaging environment. Polymers also wear and age more predictably and gradually, reducing the risk of a sudden, catastrophic failure that can damage far more than the bearing.
- Low friction coefficients help improve performance and increase component life.
- Corrosion resistance without the risk of pitting or flaking into foodstuffs. TriStar materials can even handle highly acidic products such as citrus.
- Polymers offer minimal moisture absorption. This trait helps reduce bearing expansion, even in wet environments like bottling applications.
- These materials are capable of handling high loads yet are lightweight, with a compact strength-to-weight ratio for good durability and flexible design options
- Our materials can meet appropriate industry standards for food contact applications, giving manufacturers a path to speedy, simplified regulatory compliance.
- When replacing a rolling element bearing, a single-element plane bearing offers fewer nooks and crannies for potential contamination.
- Lower lifetime TCO across a broad range of applications, essential for maximizing margins in this highly competitive industry
Food Processing Equipment
This industry uses a huge variety of specialized equipment to turn raw food into food products at scale. Because there are so many different types of food processing, the machines involved can place very different operational stresses on bearings and similar components.
Some of these machines are run almost 24/7: that’s the only way to maximize production in this high-volume industry. This means stoppages for maintenance, critical failures, and contamination problems all represent serious threats to efficient production to meet all orders in time.
Food Processing Equipment Examples: Bearing Solutions
- Fast freeze systems quickly take food products from room temperature to -112°F via a conveyorized tunnel. The bearings within the tunnel can’t be accessed for lubrication. These bearings act as the belt roller supports as the food moves through the tunnel. Rulon 641, a self-lubricating bearing material, offers a powerful solution. Rulon is FDA cleared, compatible with all cleaning solutions, and doesn’t need to be lubricated.
- Food mixers utilize different polymers depending on the media being mixed. TriStar’s polymers offer excellent resistance to long term abrasion effects. For shaft steady bearings in dry, abrasive foods, special polyolefins can be used in 40 to 180°F applications. In hot food or beverage mixers above 300°F, Rulon bearings can be used. Mixers also use polymer mixing paddles that run against the wall of the stainless tanks without abrasive wear. In one case, Rulon 641 replaced virgin PTFE in a hummus mixer and increased service life 200X
- Ovens are a huge part of many sorts of conveyorized baking, making products like tortillas, pizza crust, cookies, and bread. All of these ovens use bearings within the oven tunnel to support the conveyor belt. These belts are traditionally made from either stainless mesh or coated fiberglass. Rulon 641, fully FDA cleared, is capable of 350°F and more in continuous service. Crucially this material retains dimensional stability over a long service life of maintenance-free operation.
Food Packaging Equipment
Food packaging ranges from egg cartons to frozen food containers. Packaging encloses food to protect it from tampering or contamination from biological, chemical, or physical sources.
Innovation continues in packing technologies. Some recent examples include water-soluble packaging for liquids (like detergent “pods”), clay-based nanotechnology for fast degrading film packaging for foods, edible packaging, and antimicrobial packaging.
Equipment plays a key role in getting food inside its packaging at high production volumes. And it needs to do so cleanly and pursuant to regulatory requirements, just like the food production equipment itself.
Food Packaging Equipment Examples
- Can Manufacturing Equipment: from body makers and decorators to lid makers and neckers, these complex machines have dozens of bearing locations that require high-performance materials. These applications traditionally used bronze and nylon materials that required frequent re-lubrication. Rulon LR has successfully been used to accommodate high speeds and maintain long service life in this 24/7 production line.
- Flexible Packaging Line Equipment: these machines can handle 60,000 packages per hour and require reliable 24/7 performance for optimal volumes. Bearings, guide strips, bushings for pick and place robots, and conveyor bearings are all applications where TriStar’s materials can replace lubricated bearing materials.
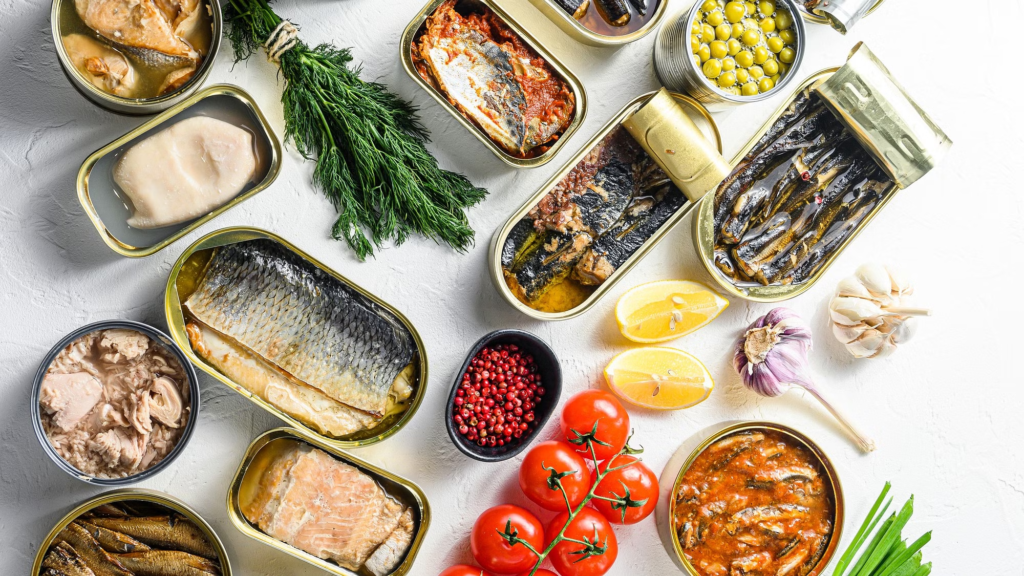
Case Studies: TriStar at Work for the Food and Beverage Industry
In many cases, TriStar has used our components to not only successfully produce components for business-critical machinery like the examples listed above but solve nagging production problems.
We provide an overview of some real-life case studies below, with links to more details.
Food and Beverage Industry Case Study One: Doughnut-Caliber Bearings
Challenge: A major baking equipment manufacturer was struggling with doughnut conveyor stainless steel bearing failure.
Solution: TriStar determined that steel bearings were deteriorating from the combination of hot oils and powerful cleaning agents. The metal was absorbing moisture and expanding to the point of failure.
We recommended Rulon 641, an FDA-cleared material with high-temperature tolerances, for conveyor bearings. Since this change, our client reports improved bearing durability and production rates.
Food and Beverage Industry Case Study Two: Production at the Speed of Dairy
Challenge: Dairy producers are always pushing to increase production speed. And with more speed comes more wear and higher temperature.
Solution: TriStar has used materials purpose-built for food production, like Ertalyte and TIVAR HOT in components ranging from chain guiders to buttermilk filling pistons. These materials have successfully enabled higher production speeds, maintained key compliances like 3A, and eliminated the need for external lubrication.